1. Determine the Brightness and Lumens Needed
Brightness is one of the most important aspects to consider when buying an LED work light. The brightness of LED lights is measured in lumens, and higher lumens typically mean brighter light. For tasks requiring
intense, focused light (e.g., auto repairs or construction), choose a work light with at least 2,000 lumens. For smaller tasks or spaces, a light with lower lumens may suffice. Ensure the brightness level is appropriate for your work environment, as too much brightness can cause glare, while too little can lead to poor visibility.
2. Look for Adjustable and Portable Designs
The design of an LED work light can significantly impact its ease of use. Adjustable designs, such as lights with adjustable heads or telescopic stands, offer flexibility and allow you to direct light precisely where you need it. If you need a portable work light, consider options that are compact, lightweight, and battery-powered. Some LED work lights also come with carrying handles or built-in hooks, making them easy to transport and position in different locations.
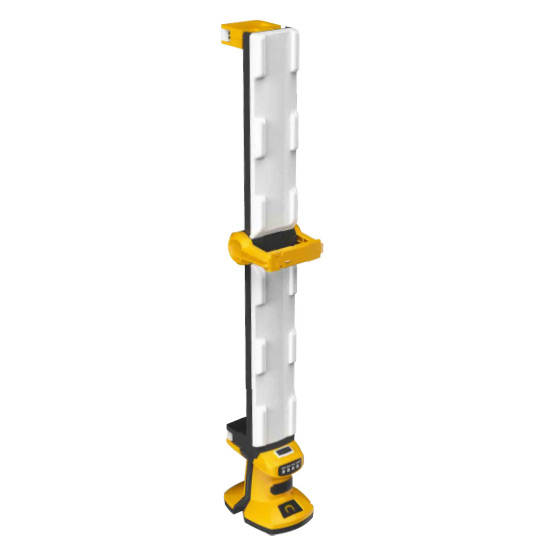
Rechargeable Multifunctional Work Light
3. Check Battery Life and Power Source Options
Work lights may be powered by rechargeable batteries, AC outlets, or a combination of both. Battery-powered LED work lights offer convenience for outdoor or remote work sites but ensure the battery life is sufficient for your needs. Look for lights with longer battery life if you need extended periods of use, or choose models with replaceable batteries for added flexibility. For indoor or continuous use, AC-powered work lights may be a better choice, as they can be plugged directly into a power source without concern for battery depletion.
4. Assess the Durability and Build Quality
LED work lights are often used in tough environments, so durability is a crucial factor. Look for models with robust construction materials, such as aluminum or heavy-duty plastic, to withstand impacts and rough handling. Waterproof and dustproof ratings, such as IP65 or higher, are also beneficial if you’ll be using the light in damp or dusty conditions. Durable lights last longer and perform reliably, even under challenging conditions.
5. Evaluate Heat Dissipation Features
LEDs are energy-efficient and generate less heat than traditional lighting, but powerful LED work lights can still produce some heat over extended use. Choose a work light with heat-dissipating features, like a metal housing with built-in heat sinks, to ensure that the light doesn’t overheat. Proper heat dissipation helps extend the lifespan of the LED and ensures safer, cooler operation for the user.

Three Head Worklight
6. Consider Additional Features for Convenience
Some LED work lights come with added features that enhance usability, such as dimmable brightness settings, adjustable color temperature, and multiple mounting options. Dimmable lights allow you to control the brightness for different tasks, while adjustable color temperature (e.g., warm or cool light) can improve visibility and reduce eye strain in different environments. Other useful features include magnetic bases, detachable stands, or swivel heads, providing more flexibility and convenience.
FAQs About Choosing an LED Work Light
Q: How many lumens are suitable for an LED work light?
The ideal lumens will depend on your specific task. For indoor tasks, 1,000-2,000 lumens should be sufficient, while larger projects, like construction, may require work lights with 3,000 lumens or more for proper visibility.
Q: Is it better to choose a rechargeable LED work light?
A rechargeable LED work light is ideal if you need portability and flexibility, especially for outdoor or remote tasks. However, for continuous indoor use, an AC-powered light may be more practical.
Q: What does IP65 mean in LED work lights?
IP65 is a rating that indicates the light is protected against dust and low-pressure water jets from any direction. This is essential for work environments exposed to dust or moisture, ensuring durability and reliable performance.
By considering these guidelines, you can select an LED work light that provides the brightness, durability, and features you need for optimal performance. Investing in a high-quality LED work light ensures safe, efficient lighting for all your work-related needs.
Looking for the best LED work lights?
At Auto Tools Depot, Find the best LED work light for you project needs. It’s important to have good lighting in the space in which you’re working. Portable work lights, LED lights for large work areas and handheld work lights are options that can brighten any work area.